Focus on Continuous Improvement
The breakthrough productivity initiative (BPI) has helped drive productivity gains throughout the Postal Service. Higher performing operations will continue to be standardized and serve as best-practice models. Value stream mapping is being used to eliminate steps that reduce efficiency and impede service. Increasingly, Lean Six Sigma tools will help apply a consistent approach to problem solving, starting with equipment and process standardization in plants. New field operational industrial engineers will play a key role to expand standardization in large plants. Over 300 field engineering positions will be filled in 2008.
A new mail processing staffing model is helping improve staffing efficiency by analyzing data from work hours, overtime, leave, and the equivalent staffing opportunities associated with processing operations. It allows managers to better respond to workload fluctuations, ensuring a better alignment of resources to mail volume, and ultimately saving work hours. Another newly-designed program analyzes productivity by comparing performance against targeted expectations.
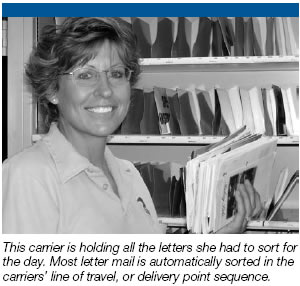
To help evaluate the day-to-day effectiveness of processing equipment, a new forecasting and scheduling model was developed to compare plan and actual production data. The information supports continuous improvement by targeting opportunities to increase processing efficiency, equipment utilization, and reduce variation.
Processes for standardizing maintenance are being developed. At select facilities, remote video maintenance support will be expanded to shorten repair cycle times, reduce maintenance costs, and improve readiness. reliability-centered maintenance (RCM) plays a critical role in preventive maintenance of processing equipment and deployments. RCM analysis will be performed on the FSS in 2008 to ensure equipment optimization.
Value-added management processes will continue to increase equipment output and improve productivity and performance. Management innovations come from both field and Headquarters sources. The mail history tracking system, developed by field managers, reduces the risk of missorted mail. The tray consolidation initiative, designed at Headquarters, improves the density of trays and standardizes and consolidates sort plans and mail flows.
3. Standardize the Use of Actionable Data
New tools are now giving managers unprecedented visibility across postal operations. Making the best use of these data and ensuring that information is actionable are essential to success. Increasing amounts of information about individual mailpieces will help pinpoint problems at the source and speed corrective action. Exception reports consolidate information and isolate major opportunities. For example, mail piece at-risk indicators are helping identify mail that is missorted or incorrectly “kicked out” of the automated mailstream. This mail requires additional handling, adding cost and sometimes contributing to delay.
The 24-Hour Clock indicators will continue to direct attention to opportunities to integrate consistency across operations. The indicators help identify where improvements are needed, from collection, through all steps in processing and transportation, to delivery. Surface Visibility continues to improve insight into mail dispatch and transportation. Information about a mailing is recorded as it first arrives at a facility, and containers are then tracked from one step to the next. Scan data is integrated with the Facility Access and Shipment Tracking appointment system to support real-time decisions on the dock. Having these data available in advance provides opportunities for more effective scheduling.
Expanded use of actionable data goes well beyond operations. Efforts to improve consistency and reduce redundancy across information systems will provide opportunities for efficiencies in other functions as well.